- The mobile flexible cable breaks: the reason is that the cable is fatigued and aged under multiple cycles of stress and high temperatures.
- Control cable disconnection: due to the long control cable and the large moving distance of the electric hoist, disconnection, and loosening of wiring are often caused by the operator’s tugging.
- The contactor contacts are burned out. For motors that repeatedly work for short periods of time, the equivalent heating current is too large. In addition, during the conversion process, the phase commutation is too fast, and the arc freewheeling of the contactor can easily cause a phase-to-phase short circuit and burn. Bad contactor contacts. For general motors, the operating current is less than the rated current. Although the starting current is 4 – 7 times the rated current, the time is short after all, and the damage to the contacts is not great. When designing the contactor, as long as the contact capacity is greater than the rated current of the motor 1.25 times is sufficient. However, the electric hoist motor is a motor with special working conditions, such as frequent starts and stops under heavy loads, reverse braking, poor heat dissipation, etc. Therefore, when selecting an electric hoist contactor, the general motor design does not conform to the actual working characteristics of the electric hoist, and burnout of the contactor is an inevitable result.
- The original limiter is driven by the displacement of the electric hoist’s rope-arranging device. Since the wire rope is relatively long (the lifting height is 25 meters), and the hook head is only 1 meter away from the electric hoist when it reaches the higher working surface, the arranging of the rope device often gets mechanically jammed, causing the limit switch to malfunction.
- The electric control box is installed on the electric hoist. The vibration generated by the machine and the frequent movement of the contactor cause the wiring to become loose. After a fault occurs, it is difficult to move the electric hoist back to the maintenance platform, which brings great inconvenience to the maintenance.
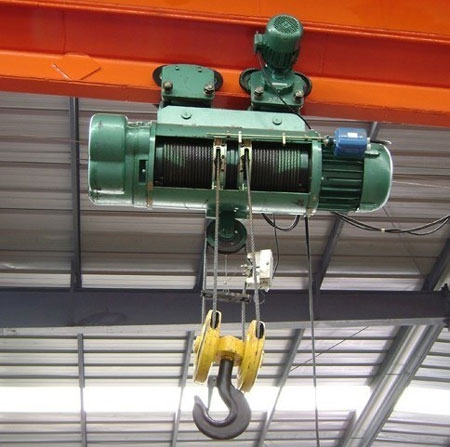
- The original mobile cable selection was not good. The ordinary YC type rubber-sheathed soft cable was used, which had poor folding resistance. Coupled with the high temperature in the factory and the unreasonable structure of the suspension pulley, the bending radius of the cable was too small, causing the cable to be damaged. Reasons for frequent damage.
Specific solutions are:
1. Use C-shaped steel rails and supporting cable pulleys. The arc-shaped carriage with the cable pulley can effectively prevent the problem of too small cable bending radius.
2. Use YGCB type silicone rubber flat cable. This cable is more suitable for frequent bending and does not kink. The silicone rubber material is resistant to high temperature and aging.
- For the issue of control cable disconnection, a better solution is to cancel the control cable and use remote control operation instead.
1. There is no issue with operation. Generally, industrial remote controls have more than 4 types of controls, and they are strictly interlocked. This is consistent with the operating requirements of the electric hoist, and can achieve up, down, left, and right operations.
2. The issue of mutual interference is not difficult to solve. We use the F 21 series industrial remote control produced by Yuding Company. This type of remote control has 4 billion sets of security codes. Only when the transmitter and receiver codes are consistent can the remote control function be realized, and there is no interference problem.
3. Solve the problem of phase short circuit. Because the inherent operating properties of the remote control are strictly interlocked, and there is an inherent delay of about 0.2 to 0.3S, only when the button pressed first is released can the button pressed later take effect.
- Replace the contactor with a larger capacity. Electric hoists have impact loads, heavy loads, and frequent starts and stops. When selecting a contactor, the two-stage capacity should be increased. For example, a 7.5KW electric hoist with a rated current of 15 A should use a 63A contactor, while the original design is only 20A.
- To replace other types of limiters, choose YBLX-10 31 type heavy hammer lever operating arm limit switch. The action principle of this kind of limit switch is to lift the weight of the limit switch through the hook head to rotate the lever, and there is rarely any jamming phenomenon.
- Remove the electric control box from the electric hoist, install it on the wall of the factory building, and fix the remote control receiver on the outside of the electric control box. This not only facilitates maintenance, but also avoids loosening of wiring caused by vibration. Use a 10-core silicone rubber flat cable from the electric control box to the electric hoist, six of which are used as load lines for the lifting and traveling motors, and the others are limit lines.
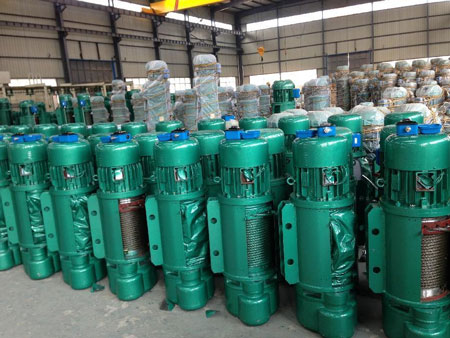
Precautions for electric hoist
- The electric hoist should be equipped with a main power contactor, an emergency stop switch should be installed near the operator, and the limit switch and other safety measures should be kept intact.
- After use, the main power supply of the electric hoist should be turned off, the power supply of the receiver should be cut off, and the key switch of the transmitter should be disconnected.
- The receiver cannot be installed in the electric control box. The correct installation method is to fix the receiver at a suitable position on the top of the electric control box, pass the receiver cable in and out of the electric control box, and make appropriate wiring to avoid interference with the electric control box, and signal interference.
- When using multiple remote controls in the same work area, be sure to use different channels to avoid mutual influence and malfunction.
Through the above modifications, the operation stability of the electric hoist has been greatly improved, and the maintenance cycle has been increased from the original half a month to more than half a year. The production efficiency has also been improved. There has not been a single failure of the electric hoist that affected the shutdown of the furnace and production reduction throughout the year.
If you have any inquiry about electric hoists, please feel free to contact us.